Company
Operations
INMATEC Technologies GmbH is specialised in the manufacture of high-utility, customised feedstocks. We develop and produce ready-to-process granulates that allow our customers to make injection-moulded ceramic components. The company is domiciled in Rheinbach, in the Cologne/Bonn region (Contact and Map). Our feedstock production, development division and consultancy experts for ceramic injection moulding are all located there at a single facility (Products & Services).
Service and quality are our top priorities. Prior to use, our incoming raw materials are rigorously inspected. Each feedstock batch we manufacture is subject to exhaustive quality testing. Certified according to ISO 9001:2015, we guarantee the consistent and reproducible quality of all products and services.
We make standard feedstocks and can also offer the development of customised products. Material selection, the composition of ceramic powders and binder components are tailored individually to the requirements of the component and application. INMATEC Technologies GmbH blends knowledge and experience with technical consulting on all productive aspects of the injection moulding process.
We team up with our customers to develop end-to-end component solutions for the most varied of applications and scenarios, for instance in the electronics, automotive, aeronautics & aerospace and household appliances industries. Transparent information and support are the key competencies that we uphold to build close and successful partnerships with our customers.
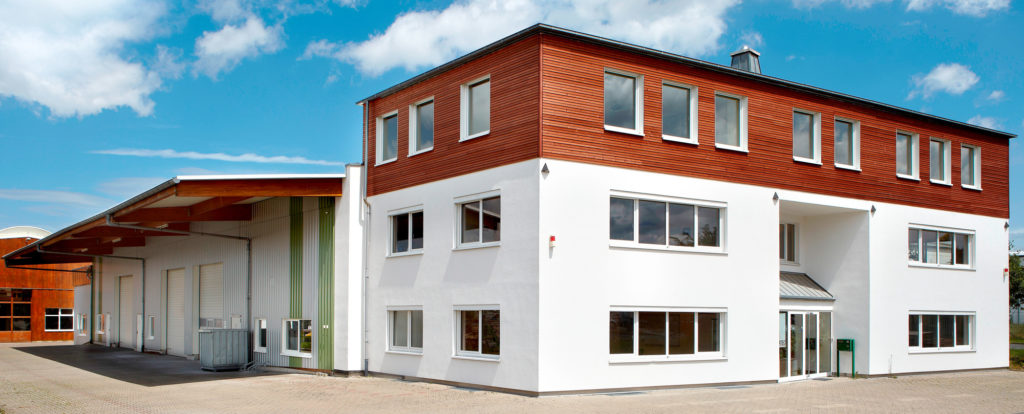
At a glance
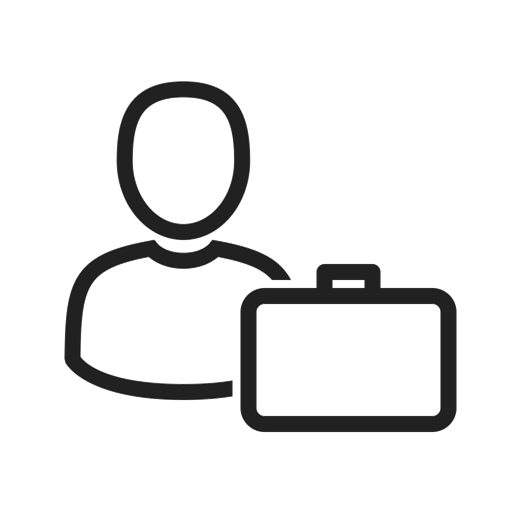
Management:
Dr Moritz von Witzleben
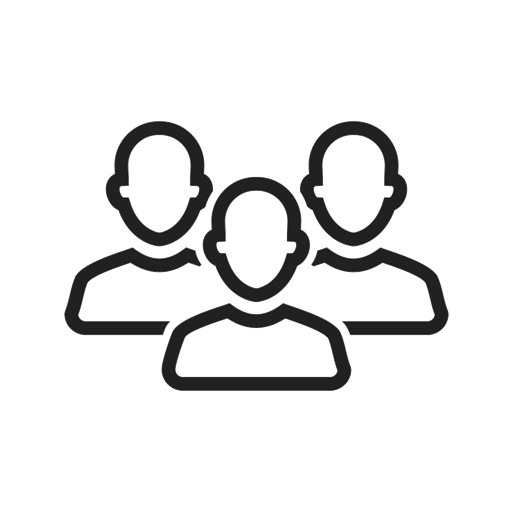
Workforce:
Around 50 employees
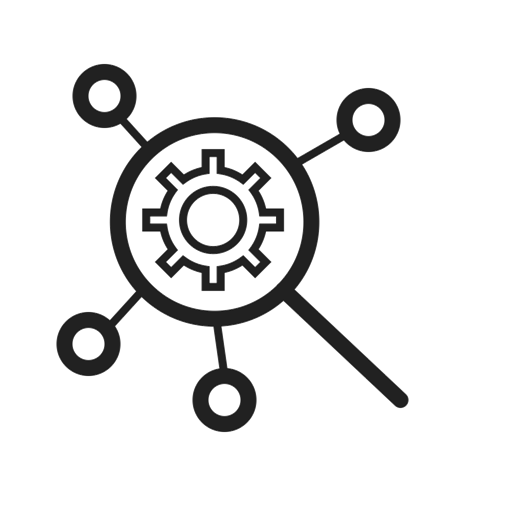
Core competencies:
Ceramic feedstocks
Ceramic injection moulding
Technical ceramics
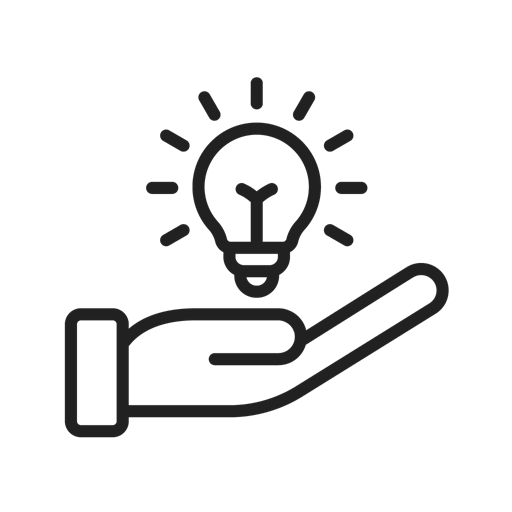
Services:
Development
Production
Consulting
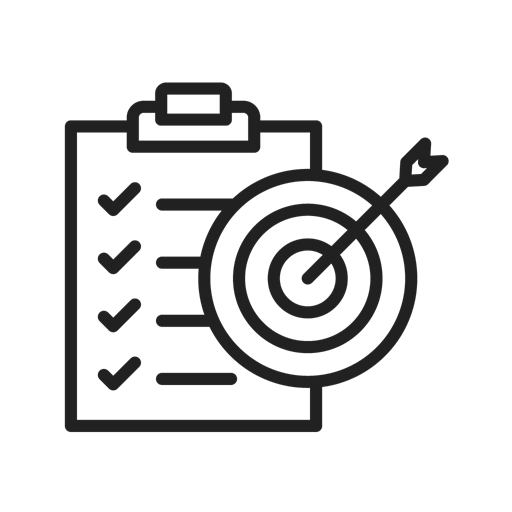
Key market:
Automotive industry | Textile industry | Jewellery industry | Dental technology | Electrical engineering | Sensor technology | Medical engineering
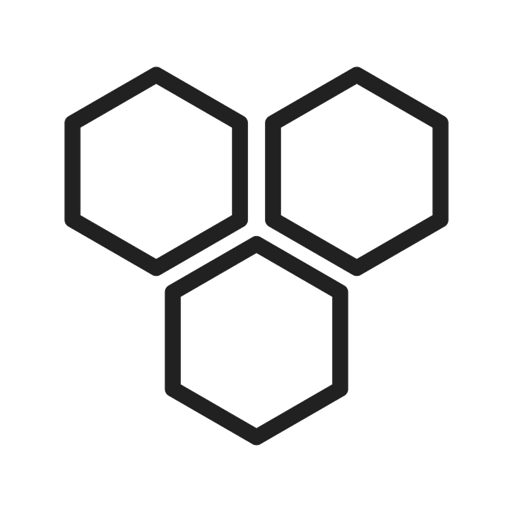
Binder systems:
INMAFEED
INMAFLOW
INMAPOM
Customised options
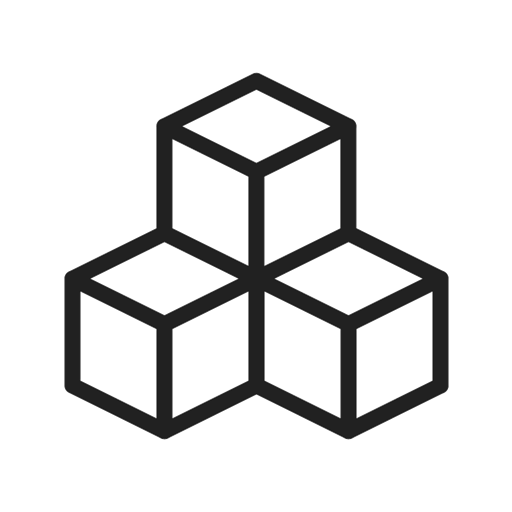
Ceramic types:
Aluminium oxide | Zirconium oxide | Zirconium oxide-reinforced aluminium oxide | Aluminium oxide-reinforced zirconium oxide | Non-oxide materials
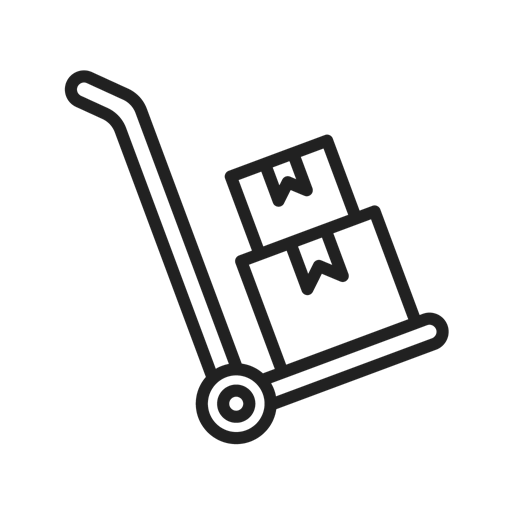
Product range:
Standard feedstocks based on the three binder systems | Customised feedstocks
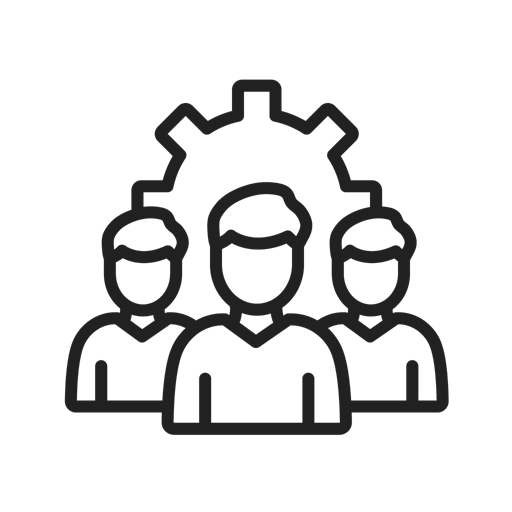
Production:
3-shift system
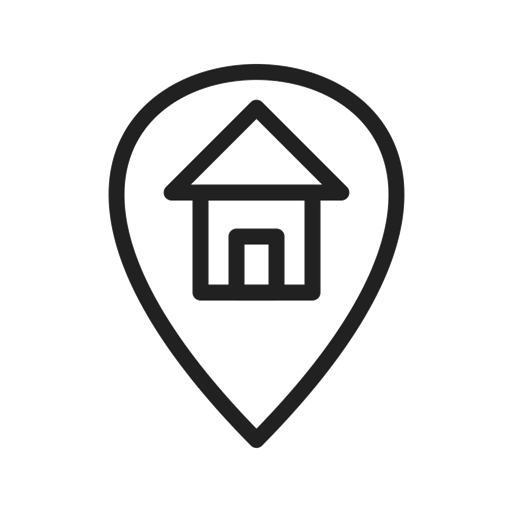
Floor space:
Approx. 1,450m²
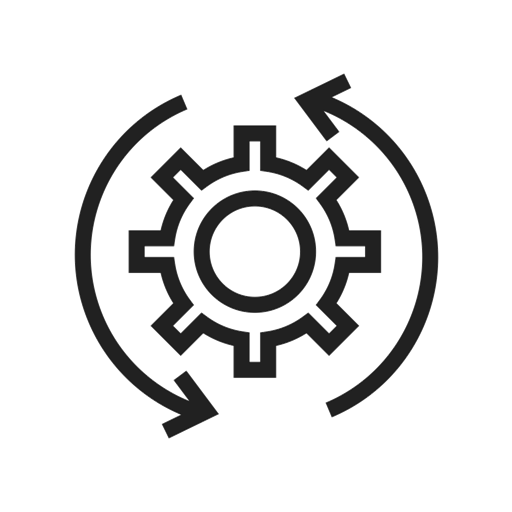
Processing units:
8
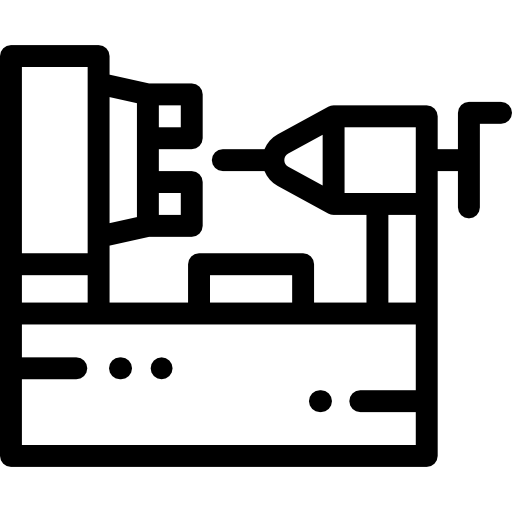
Injection moulding machines:
2
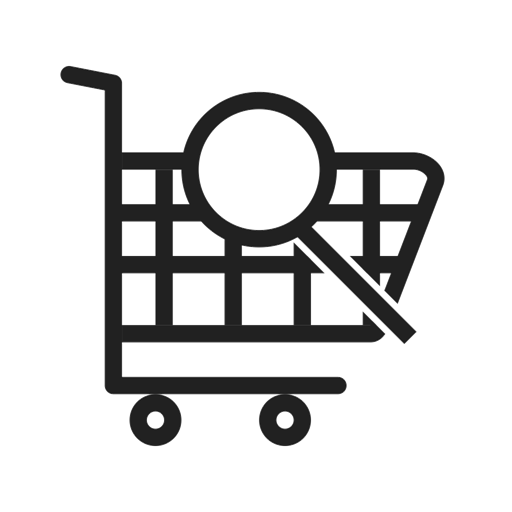
Customer base:
Worldwide
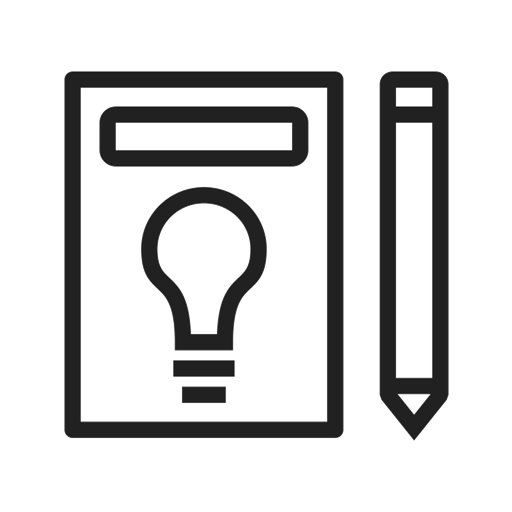
Annual certification:
ISO 9001:2015
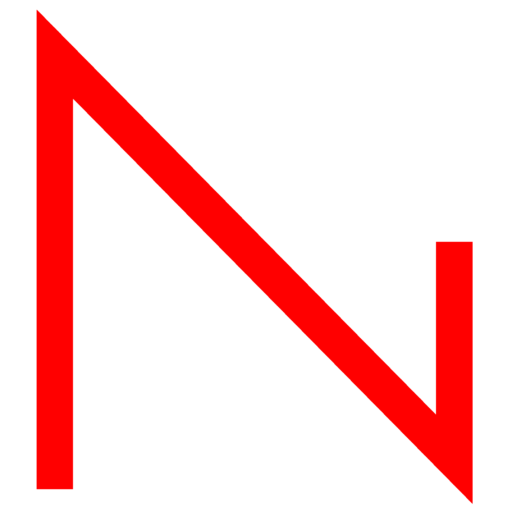
Our history
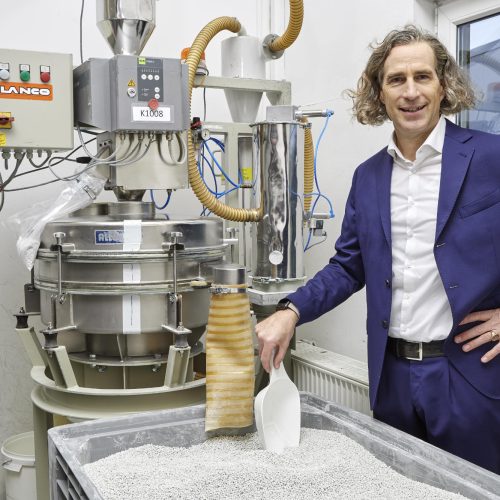
1998
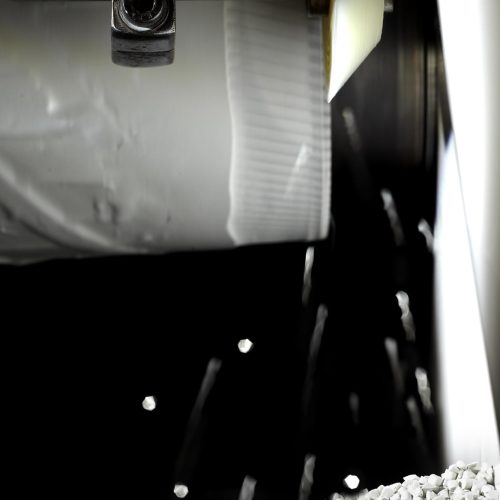
1999
Rheinbach
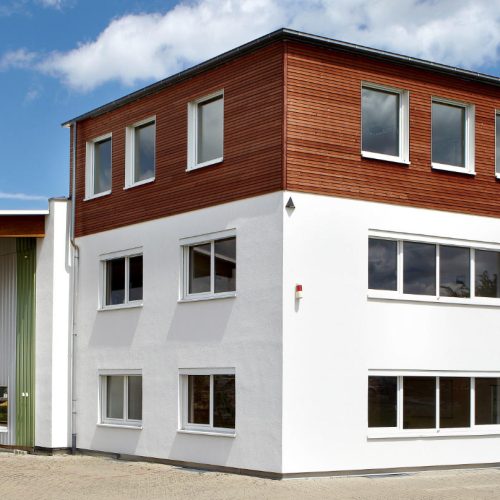
2001
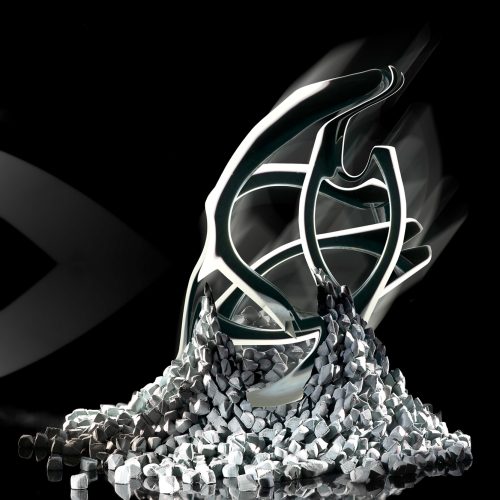
2006
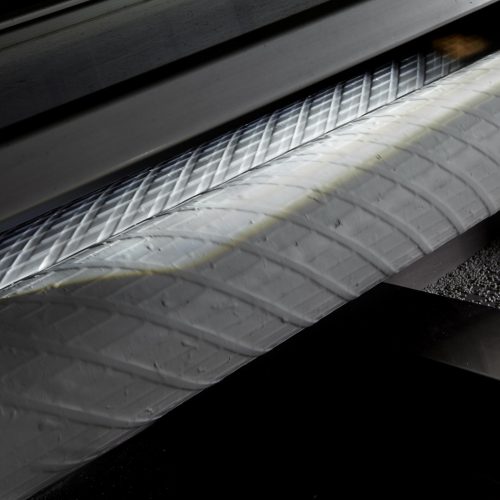
2012
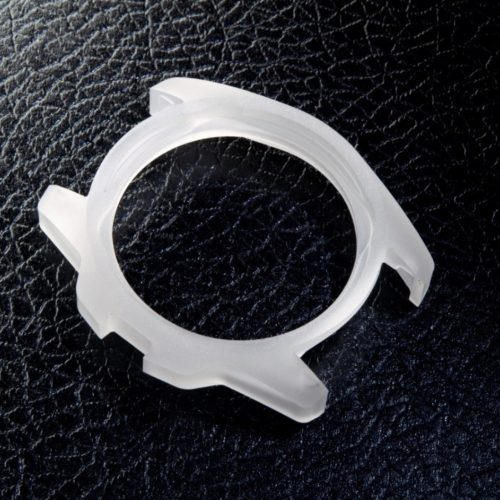
2013
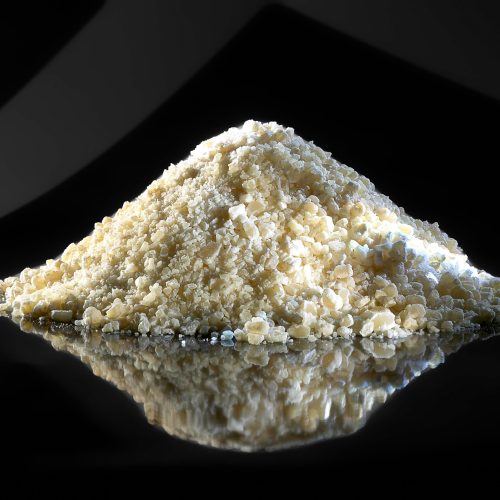
2014
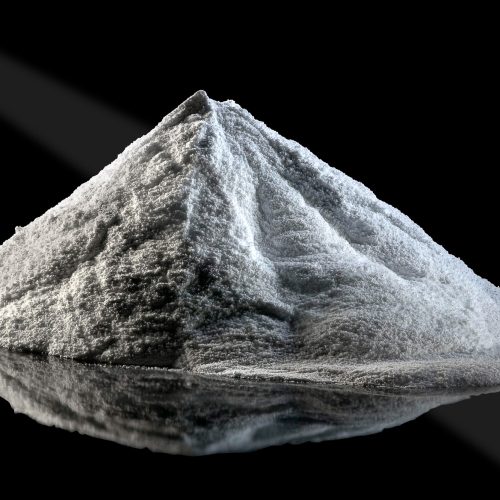
2017
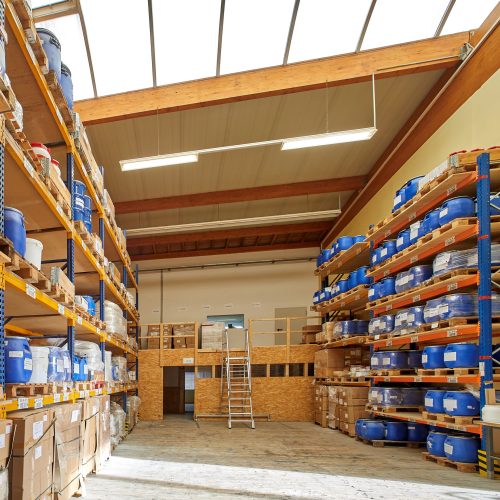
2020
Team
Introducing INMATEC – get to know our management team, feedstock experts and material specialists.
Professor Moritz v. Witzleben, PhD
Stephan Jegust
Marvin Retterath
Dr Markus Zwick
Vanessa Reinecke
Thorsten Münch
Commitment
We are committed to developing the industry, even beyond our own company. Driving the development of powder injection moulding is the declared objective of INMATEC Technologies GmbH. This prompts us to collaborate with other companies in several expert committees and professional organisations, in which we have been involved for many years. These alliances enable us to continuously advance the knowledge and opportunities that the process can offer to the modern industrial sector.
German Ceramics Society
DKG is the port of call for practical applications, teaching, research and industrial enterprises operating in the field of ceramics. Europe’s largest organisation in this field, it promotes research and development into ceramics.
Expert Panel for Ceramic Injection Moulding
The German Expert Panel aims to continue developing the entire process chain of ceramic injection moulding in order to leverage component precision, process reliability and economic efficiency.
Expert Group on Metal Injection Moulding
The Expert Group on Metal Injection Moulding (MIM) is a technical working body within the Joint Committee on Powder Metallurgy. The group consists of industrial partners and research institutions.
European Ceramic Society
ECerS is the alliance of national ceramic associations in Europe. It advocates progress in science and research, as well as the promotion of junior professionals and international collaboration.
Sustainability
INMATEC has adopted sustainable practices.
In addition to meeting the highest quality requirements for our products and services, it is also our declared goal to fulfil our responsibility towards the environment and future generations. From the perspective of sustainability, INMATEC focuses on the efficient use of resources, minimising energy consumption and on the avoidance of waste along the value chain.
Sustainable action has long since become an integral part of our daily routines – from our binder systems that ensure eco-friendly de-binding, to the recovery and recycling of residual materials during production and the shipping of feedstocks in reusable containers. We join with our partners and staff to put our goals into practice and to continue improving sustainability management.